High vacuum
Turbo pumps and vacuum technology
Is your business in need of a high vacuum pump? A high vacuum means a molecular flow with very little matter, because the pressure is very low. All matter – even gas – has a small vapour pressure and even this vapor pressure needs to be lowered to create high vacuum. In order for the pressure to drop below the vapour pressure of matter, it is not possible to use traditional mechanical movement of gas, but other methods need to be used.
Low2High offers several variants of high vacuum pumps for the really low pressure levels:
• Turbo molecular pumps – also called turbopump. Only used with a pre-vacuum pump to create a very low pressure.
• Cryogenic pumps/cold head compressors – capture gas molecules in the vacuum chamber, by attaching them to cryologically cooled surfaces.
• Diffusion pumps – a vacuum system that uses steam to transport gas out of the vacuum space at high speed.
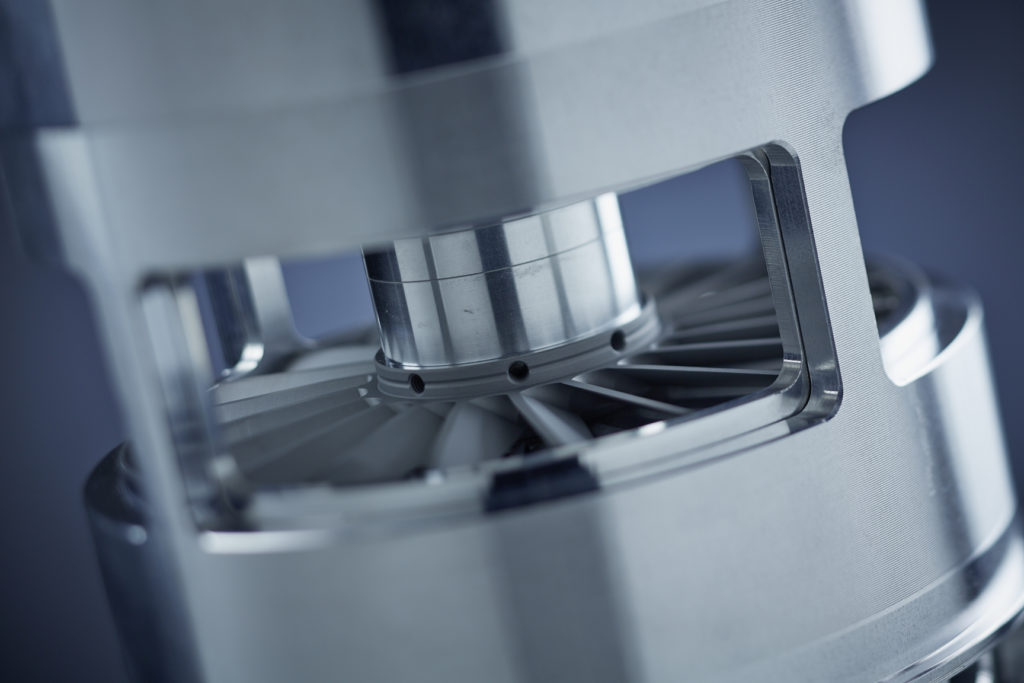
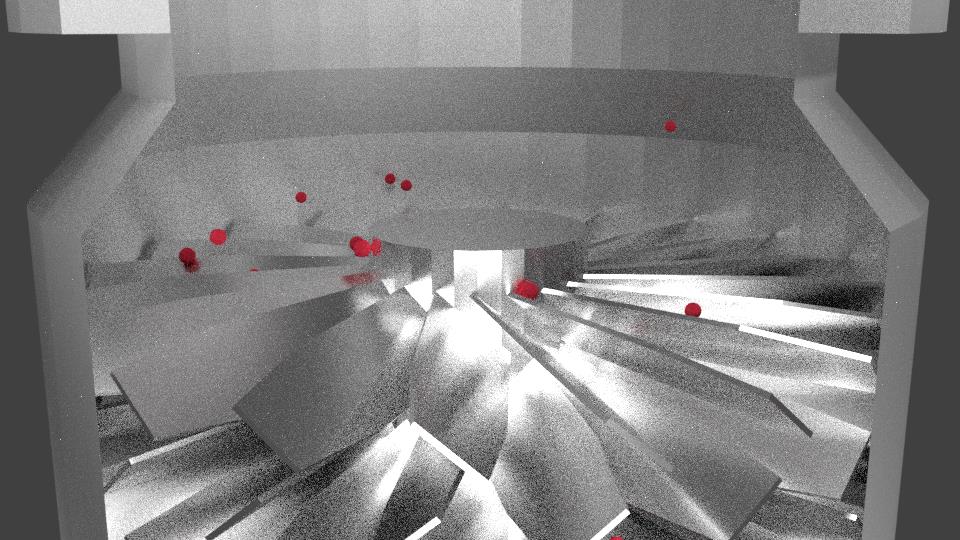
Turbo molecular pumps (turbopumps)
Turbomolecular pumps or ”turbopumps” as they are colloquially called are high vacuum pumps that are only used in combination with a pre-vacuum pump. The pumps are generally used in applications that require a clean operating environment under high vacuum or ultra high vacuum. The principle of operation of a turbopump is that a turbine spins at high speed in a pump housing where most rotor stages in the turbine are equipped with rotor blades. Between each stage of rotor blades, there are stationary stators that are angled in the opposite direction to the rotor blades, forming a ”V” shape between them.
Using the kinetic energy through the turbine’s rotor blades, the rotor blades strike the gas molecules in an axial direction down through the pump body.
For each rotor stage and stator stage, the molecules are passed through the pump in the direction of the pre-vacuum flange.
During molecular flow (<10-3 mbar), the mean free path (the distance that a molecule travels before colliding with another molecule) of gas molecules is greater than the distance between rotor and stator blades (normally a few tenths of a millimeter).
This means that the molecules instead collide with the closely seated rotor blades and result in a very efficient pumping speed.
On some models, you also have an extra compression step that has slightly different names depending on the manufacturer and variants of the same type of solution. Sometimes it is called ”drag stage”, sometimes also ”Siegbahn stage”we usually call it ”Holweck stage” after the inventor.
This additional compression step adds another dimension to the pump type in terms of the pressure at which the pump can be started.
With a Holweck stage, the pump can start even at pressures as high as 10-15 mbar (N2).
Another thing that is usually important for users is the types of bearings that the rapidly rotating turbine uses.
The older models had regular grease or oil-lubricated bearings to be able to last a long life. Over time, it became increasingly important for users of the pumps to limit the potential risk of contamination of the vacuum system as a result of hydrocarbons from grease and oil managing to escape their encapsulation through the pump and find their way in (against the flow direction) into the vacuum system and potentially destroy products or samples that were in there.
In order to overcome this problem, alternative solutions to the problem were developed. Magnet-bearing turbopumps.
The new ”MAG” pumps had magnetic bearings that do not naturally have any contact with the rotating turbine, thus limiting potential leakage. The only time that the bearings are subjected to mechanical wear in the classical sense is when the pump is stopped and when the lower part of the turbine ”lands” against the bearing surface and makes contact. However, this is a minor wear and tear in this context and the technology with magnetic bearing is classified as a major advance in terms of service life of turbopumps.
In recent years, the two methods have begun to be combined to further extend service life and reduce downtime; Historically, when the pump has broken, it has always been necessary to send it to a workshop with the right skills and the right tools to be able to repair the pump.
The modern solution is called hybrid pumps where you have taken a magnetic bearing located in the upper part of the pump, and supplemented this with a permanently lubricated bearing in the lower part of the pump. With the experience of the users who thought it was complicated and expensive to send the pumps for repair to workshops, this was taken to heart and also solved the problem with the most common breakdowns so that these could be fixed on site with the users instead. Nowadays, the new standard on the market is hybrid pumps for their versatility in terms of pumping ability and long service life.
Turbomolecular pumps can be found, for example, in these contexts:
- Analysis instrumentation
- Leak detection/mass spectrometry
- Gas chromatrografi
- Quadrupol time of flight (Q-TOF)
- ICP-MS
- MALDI-TOF
- Electron beam microscopy
- Coating
- Data storage (optical)
- Data storage (magnetic)
- Flat Panel Manufacturing
- Optical coating
- Decorative coating
- Metallization
- Protective films
- Metallurgy
- Research and development
- Surface analysis
- UHV/XHV systems
- Particle accelerators
- Fusion experiments
- Space simulation
- Semiconductor processes
- Load lock and transition chamber
- Etching
- PECVD
- PVD
- Jon planting