Freeze-drying
Freeze-drying
Freeze-drying is mainly used to preserve or store temperature-sensitive products: the advantage of this method is that the product would lose essential and desired properties if preserved or dried by other methods.
The application of freeze drying is mostly in industries such as pharmaceutical,
biology and medicine. But freeze-dried food is also available.
A perhaps slightly odd application may be the conservators at museums who used
And maybe even now they apply freeze-drying to their stands of, among other things, reptiles.
Now in recent years, even florists have discovered freeze-drying.
They offer freeze-drying of, among other things, bridal bouquets.
From a purely process technical point of view, it is characteristic of freeze-drying, that water is removed from
a frozen solution or/preparation without thawing, in other words by sublimation. Sublimation, which is the process where the solid phase transitions directly to a vapor phase, i.e. skip the liquid phase. The liquid-to-vapour phase transition that usually occurs in normal drying is replaced by conversion first from the liquid to the solid phase (freezing)
followed by the solid-to-vapour phase (sublimation or freeze-drying in the strict sense of the term).
Thereafter, a so-called post-drying takes place where you evacuate further to
evacuate or degas the so-called non-condensable gases.
The most important phase of the process is actually the freezing phase.
It determines the crystal structure of the finished dried product
or have for function. The crystalline structure, solubility, activity, life force
And the color of the product is affected by the freezing process.
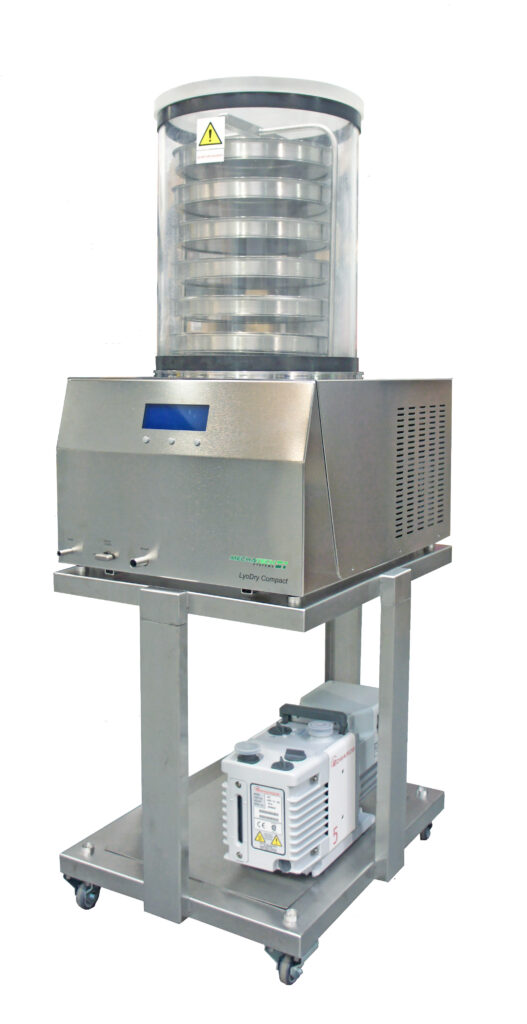
As can be seen from the phase diagram of water, all three phases are in equilibrium at the so-called ”triple point”. When an aqueous solution is cooled, the crystallization of water in most cases begins below freezing (0 ° C). At the same time, it should be noted that all substances have a triple point or eutectic point and that the values of this triple point differ considerably. This can be seen most clearly if you use ”plain water” and add a little salt.
The most common freezing method used in laboratories is a regular freezer box
or freezers. The requirement is about -60 degrees C but preferably -80garder C.
The lower the temp, the smaller the ice crystals, the better
the end result of the entire freeze-drying process.
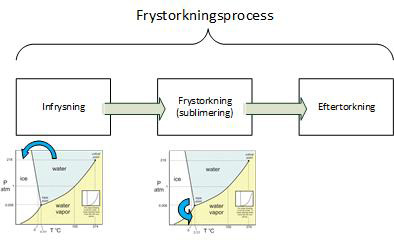
The two main freezing methods used for pharmaceutical products:
1. Freezing on contact with a cooled surface, the product plate
2. Rotary freezing in cooling water baths; Spin freezing and peel freezing technique.
There is no general rule for the large number of products that can currently be freeze-dried.
Some of them require slow freezing, and others faster
freezing to achieve a high-quality end product.
We will only deal with so-called laboratory freeze dryers in this section. Mainly due
that we have limited ourselves in our program of larger and fully automatic plants for freeze dryers. However, we are happy to convey inquiries.
The freeze-drying plant consists of a chamber connected to a condenser
and a vacuum pump. Usually, the condenser is cooled via a chiller, which in laboratory facilities usually has a final temperature of -53 degrees C. A distinction is made between single-chamber and two-chamber freeze dryers. This is because you want to be able to determine the end point of the drying process. This is done by means of a valve, separating the chamber from the cooling condenser. With the help of a pressure sensor of the Pirani type, it is then possible to determine the temperature of the ice core using barometric methods. In this way, set their own dryness limits.
If you do not have products of this type where the final drying level is important, a single-chamber freeze dryer can advantageously be chosen. It is both cheaper and easier to handle.
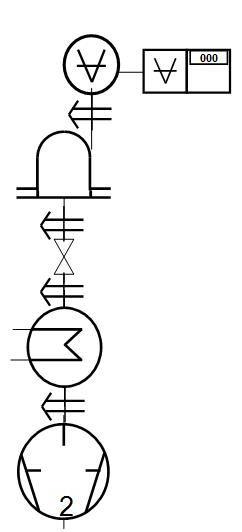
Sublimation drying
At the beginning of drying, sublimation of the ice occurs at the surface.
As the process progresses, the sublimating excess draws into the product, and the developing steam must be passed through the previously dried outer layers. Therefore, drying depends on the speed of steam, transfer and removal, as well as the necessary sublimation heat.
The heat required for sublimation is supplied to the product by convection and heat conduction, and to a small extent by heat treatment. In addition to heat transfer through heat conduction and radiation, it is most important that heat transfer by convection is optimized. However, it must also be taken into account that due to reduced pressure in the drying chamber, convection will practically cease at a pressure below 10-2 mbar.
The product dries on the surfaces that can absorb heat. As drying continues,
pulls the ice core into the center of the product.
To avoid damage to the product, the maximum allowable temperature for it is allowed
dried product not exceeded. On the other hand, care must be taken to ensure that the product is not damaged by thawing.
In order to achieve rapid and effective freeze-drying, it is therefore necessary to ensure:
precise temperature control on product shelves, as well as partial pressure and total pressure control
in the freeze-drying apparatus or plant.
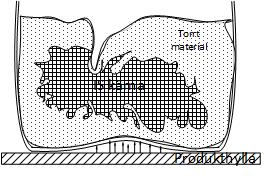
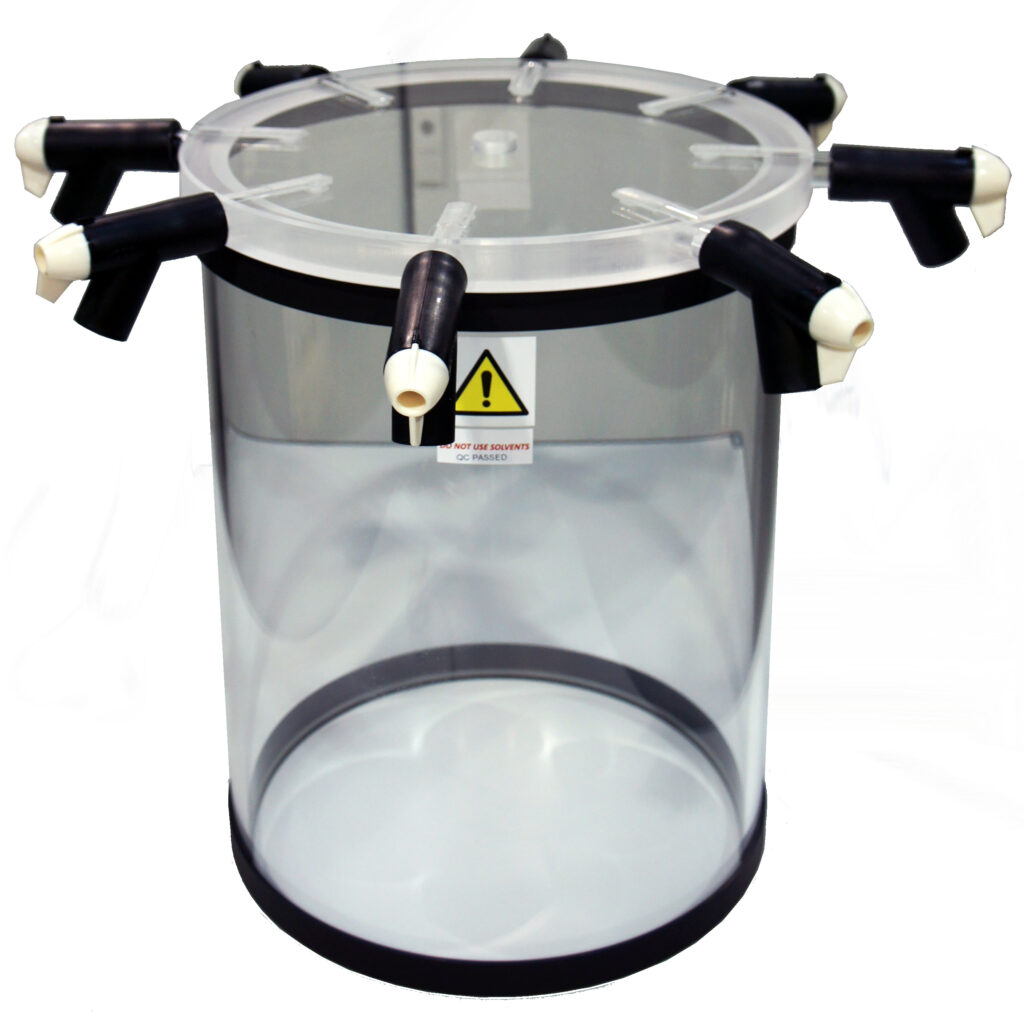
The post-drying process
In the final drying phase, the water bound by adsorption must be repositioned.
To achieve this, it is often necessary to overcome the capillary forces of the water and a freeze-drying plant must therefore be designed to provide a high-pressure gradient during the final drying phase.
This can be done by lowering the condenser temperature below -70°C, the pressure conditions are produced that allow secondary drying of the products to a low residual moisture content.
There are many good reasons for a close observation of the drying process, especially for determining the end point of the drying process. It may seem that weighing the product may be a possible method for determining the loss of water during the drying cycle. In the ultimate drying phase, however, this method would be of little use, as the amount of water vapor still sublime will be too low for measurement. Although the method can be used in a laboratory, it is not suitable for industrial production.
Another method is to monitor the temperature, which, however, requires extremely precise arrangement of the sensing probes and virtually identical conditions at all measuring points.
Normally, the temperature probes are too large and thus give measurement errors that increase with size. However, the usual disadvantage is that the product temperature can only be measured at one or two points.
The most reliable and accurate technology is the pressure stepping method (barometric temperature control) developed and patented by LEYBOLD-HERAEUS.
Due to the pumping effect of the ice condenser, the partial pressure of water vapor during the drying process always remains below the saturation vapor pressure corresponding to the sublimation temperature.
When the condenser is isolated from the chamber, which, of course, must be vacuum tight, the flow of steam to the condenser is interrupted, and the partial pressure of water vapor rises within a very short time to the equilibrium pressure, which is indicated by the vacuum pressure sensor. Towards the end of the drying process, the pressure increase gradually becomes smaller, due to the smaller amount of steam released by sublimation. When the pressure rise (pressure rise) ceases is complete and the drying process can be completed. There are no ice cores left in the product. This, of course, applies, provided that the apparatusis vacuum-tight.
Finishing
The final dry products are very hygroscopic. The dried products must be protected after drying. If the product is dried in bottles, bottles or bottles, it seems logical to close these containers immediately after drying before removal from the plant.
For this purpose, special ribbed/grooved rubber stoppers are placed in the neck of the bottle or bottle, before drying and, at the end of the drying process, pressed firmly into the neck of the bottle with a sealing device,/(”stuffing-device”)
The containers can be sealed under vacuum or under shielding gas atmospheres – nitrogen or other inert gas. The method used depends on the type of product and the quality of the rubber stoppers.
Products for Freeze Drying Applications
We are happy to assist with application tips when it comes to choosing the right dryer that can be expandable and modifiable for future use.
The main questions that we will ask at first contact are:
What solution/reconstitution will be available?
Is it just water?
How much water/ice will need to be dried per batch?
What Method Will There Be Bulk/Flat Barrels/Bottles/Pistons?
One or more shelves?
Head over to our freeze-drying prospectus to get an idea of the different models available.
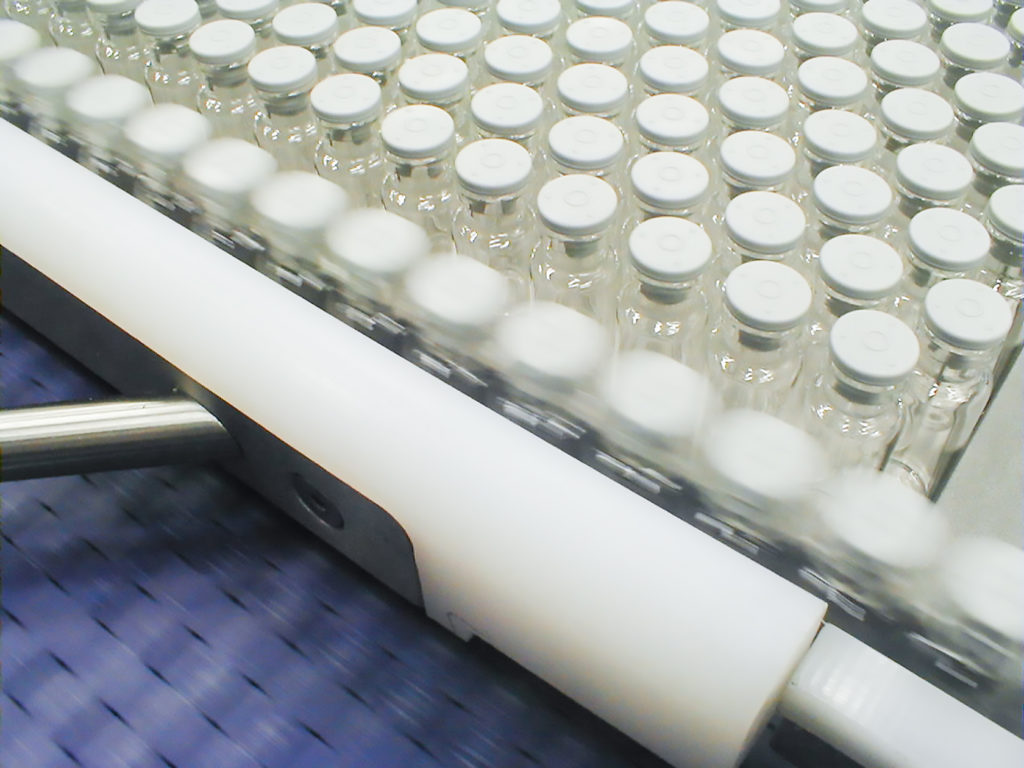
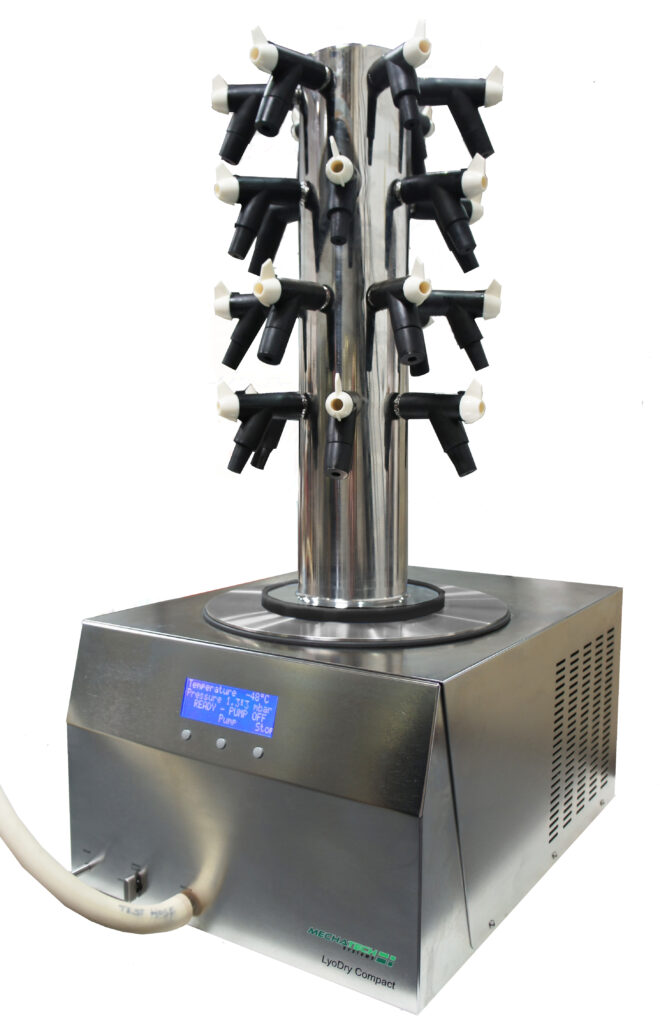
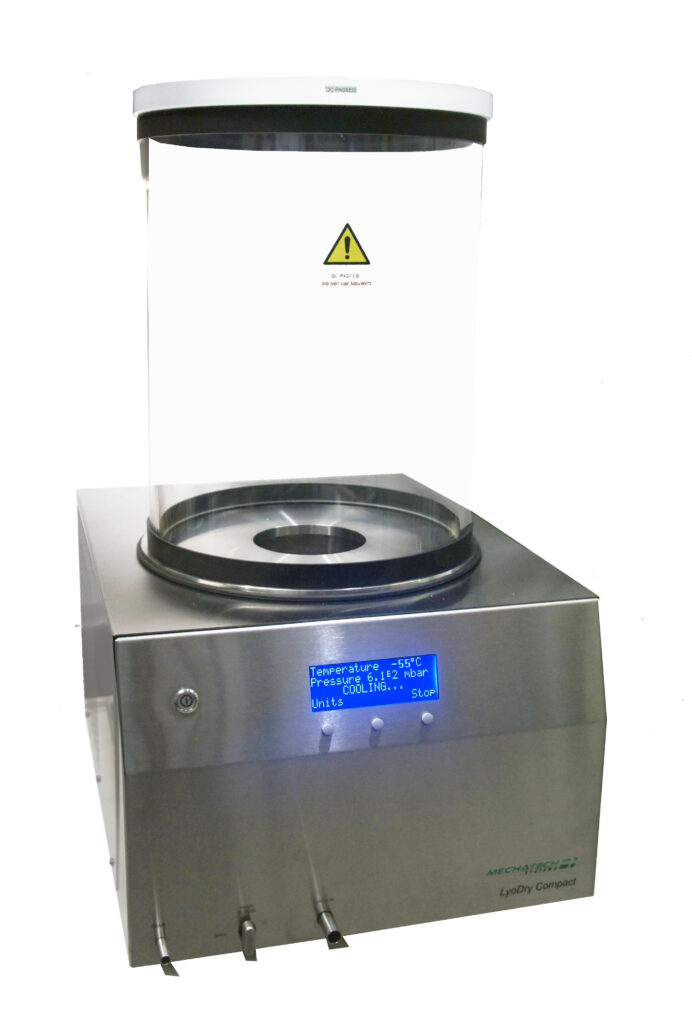